- Pressure
- Level
- Flow
- Gas Detection
- Signal Conditioners
- Temperature
- Fluke Test Tools
- Combustion and Gas Analyzers
- Compressed Air DryersCompressed Air Dryers
- Filtration
- Heat Trace & Electrical Heating
- Mass Flow Controllers
- Miniature Pumps, Valves & Controllers
- Moisture Analysis
- Nitrogen Generators
- Oxygen Analysis & Inerting Control
- Pressure Regulators
Mass Flow Meters and Mass Flow Controllers
Parker’s comprehensive line of mass flowmeters and mass flow controllers deliver precise, dependable mass flow measurement of air or other gases. Engineered with Parker’s expertise in thermal mass flow, these flowmeters feature our most advanced sensor, valve and laminar flow element technologies. Providing unrivaled levels of accuracy, Parker’s mass flow controllers can detect, measure and control mass flow rates, from very low to very high mass flow velocities
Parker X-Flow Mass Flow Controller
The Parker X-Flow™ is a streamlined Thermal Mass Flow Controller that controls flow from 0.8 ml/min to 20 l/min with a 1% accuracy & a max pressure of 145 PSIG. X-Flow™ delivers fast, repeatable and reliable high accuracy flow control through proven Constant Thermal By-Pass Mass Measurement technology coupled with our most popular digital communication protocols. X-Flow™ is calibrated to your specific conditions and includes the Parker Tracking system that assists with your annual asset calibration needs, delivering a higher level of productivity, efficiency and reliability.
X-Flow Mass Flow Controller Brochure
X-Flow Mass Flow Controller Datasheet
Features/Benefits:
- Aggressively priced for OEM applications
- Flow ranges from 0.8 ml/min to 20 l/min
- Fast, Repeatable and Reliable Performance
- Premium Accuracy with Proven Thermal Mass Flow Sensor and
Laminar Flow Element
- Great low range flow measurements
- Easy to integrate into your new or existing systems
- Asset calibration management software included
- Cleaned for Analytical Use
- CE, REACH and RoHS II
Markets:
- Laboratory and Process Instrumentation
- Pharma/Bio-Pharma Equipment
- Air Quality Monitoring System
- Furnace and Coatings
Applications:
- Gas Control for Laboratory and Process Equipment
- Burner Ratio Control for Ceramics and Metals
- Process and Environmental Analyzers
- Emissions Monitors and Calibrators
Parker Series II Mass Flow Controller
Our Series
II thermal mass flow controllers & flowmeters offer outstanding value in a
wide range of applications. Exceptional accuracy
for flow ranges from 0.014 sccm to 1,670 slpm, with high precision and <0.2% repeatability. Rated for 8 separate gas types which are field adjustable. Our thermal mass flow controller is available
in both digital and analog styles, fully compatible with RS232 and digital
protocols such as Profibus. If you're
not sure what gas you're going to use or your process changes, our MFC allows
you to migrate to a new gas within your flow range without purchasing a new
mass flow controller. Parker's highly
precise mass flow controllers provide you the diagnostic stability, repeatability,
and flexibility you need for low flow gas applications.
Series
II Mass Flow Controller Brochure
Series
II Mass Flow Controller Datasheet
Features/Benefits:
- Gas flow ranges from 0 - 0.7 ml/min up to 0 - 1670 l/min
- Operating pressures up to 5800 PSIA
- High accuracy and repeatability
- Storage of max. 8 calibration curves
- User configurable control characteristics
- Flow Parameter Adjust functionality up to 150 PSIA
- Effective rangeability <150:1
- Analog or digital: RS-232, DeviceNet™, Profibus-DP®, Modbus-RTU™
Markets:
- Laboratory and Process Instrumentation
- Pharma/Bio-Pharma Equipment
- Air Quality Monitoring System
- Furnace and Coatings
Applications:
- Gas Control for Laboratory and Process Equipment
- Burner Ratio Control for Ceramics and Metals
- Process and Environmental Analyzers
- Emissions Monitors and Calibrators
Principle of Operation
Parker Model 201 Mass Flow Controllers (MFC) incorporate an operating principle based on the thermodynamic properties of the process gas being measured. Mass flow measurement relates to the amount of heat absorbed by the process gas. The amount of heat the gas absorbs is determined by the gas molecular structure. Specific heat, the amount of heat required to raise the temperature of one gram of a given gas one degree centigrade quantitatively describes this “thermal absorbency”. Mass flow measurement consists of a bypass sensing tube with a heater wound around the center of the sensing tube and precision resistance type temperature sensors located equidistant upstream and downstream of the heater. A laminar flow element package, located in the main flow stream, acts as an appropriate restriction creating a pressure drop forcing a fixed percentage of the total flow, approximately 10 sccm, through the bypass sensing tube for temperature differential detection. As gas flows through the sensing tube, heat is displaced to the downstream temperature sensor creating a temperature differential between the upstream and downstream temperature sensors. The upstream and downstream temperature sensors form two legs of a bridge network at the sensor assembly inputs to the PCB. The resulting temperature differential is amplified on the PCB assembly to a 0-5 VDC output signal directly proportional to the gas mass flow rate. To ensure an accurate flow measurement, flow disturbances must be eliminated or greatly reduced. Accordingly, both the sensor tube and the laminar flow element package are designed for laminar flow. Actual gas or gas factors are used in calibration to account for the specific heat of the measured gas.
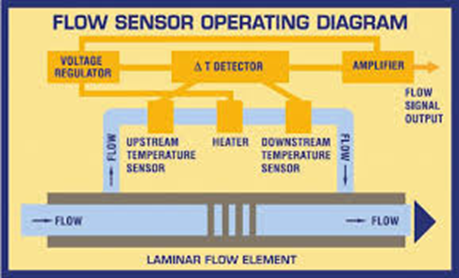
Powered By Mshop360.com
RJM Sales © 2024